Arc pulsing involves four welding parameters; Peak current, background current, pulse width (duty cycle or percent – on – time), and pulse frequency (pulses per second). Although the parameters are most often chosen and changed according to the specific needs there are some industry standards that have been developed as starting parameters. Experimentation and experience will determine the final weld parameters chosen.
Step One : Average Current Required : Using the power supply in the unpulsed mode, establish the weld current required to melt and fuse the materials to be welded. Some times this weld current can be calculated using the 1 amp per 0.001” of material thickness rule. Example: If the material thickness or depth of weld penetration is 0.060 then 60 amps of average weld current will be required. Continue to increase the weld speed and current until a point where the arc and weld are still giving consistent results.
Step Two : Peak and Background Current Settings : The average current will be effected both by the peak to background current ratios and the duty cycle/pulse width (the percentage of time spent on the peak current setting) As before, these settings are changed according to the specific needs of the application. Peak to background current are normally in ratios of 2 – 5 and pulse widths are often 20% to 50%
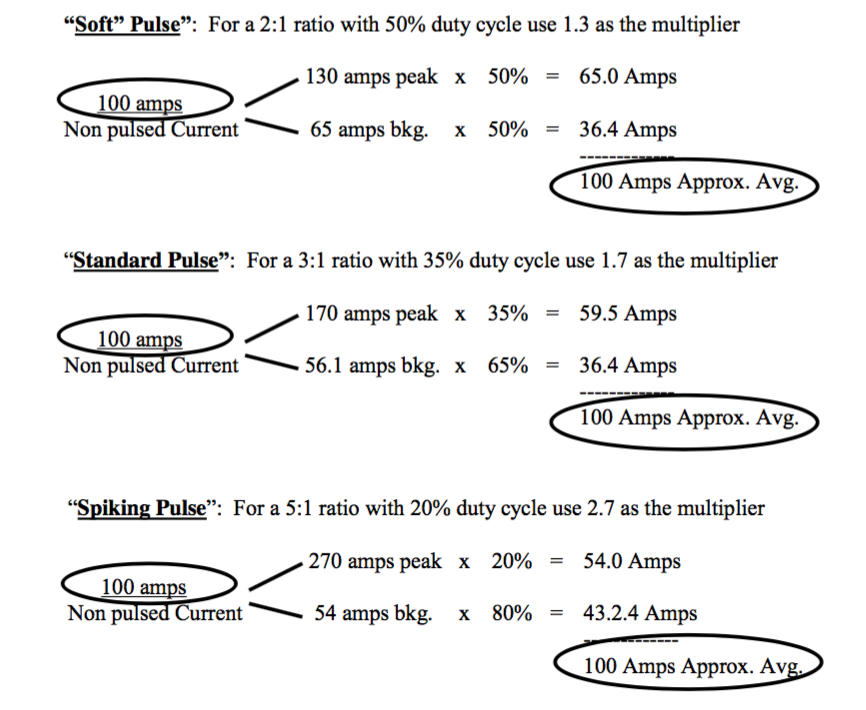
If necessary a ballpark starting value can be pre – calculated using the following formula:

(Hz or Pulses Per Second) Inches per pulse (distance between pulses)
Example: Stainless steel material of thickness 0.060” being welded with a travel speed of 10 i nches per minute (0.16 inches per second) and a desired spot overlap of 75%. The weld puddle size will probably be 2.5 times the wall thickness (depending on any tooling used) so the distance between spot edges will be (2.5 x 0.06 x (1 – 0.75)) = 0.037

Many times, for thin wall or shallow penetration the starting pulsation rate will be half the travel speed in IPM. In the example above the travel speed was 10 IPM and the starting pulsation rate could be taken as 5 PPS
Varying the pulsation rate may also give a more stable arc for a given set of parameters and thus more consistent weld results. Experimentation and experience will determine the final weld parameters.